Teknol.eu
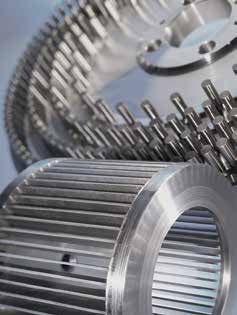
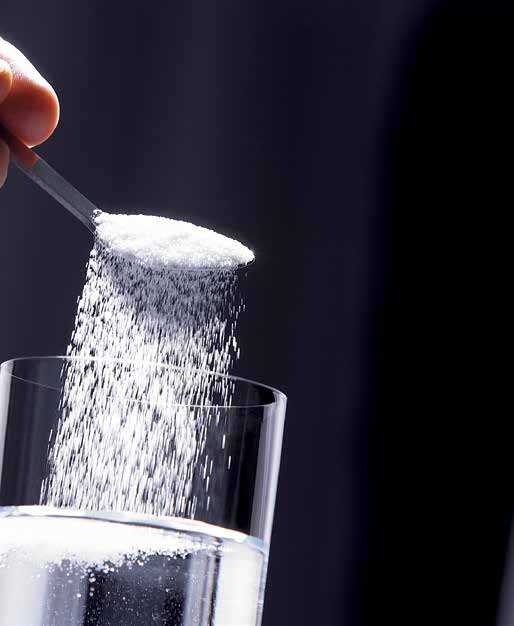
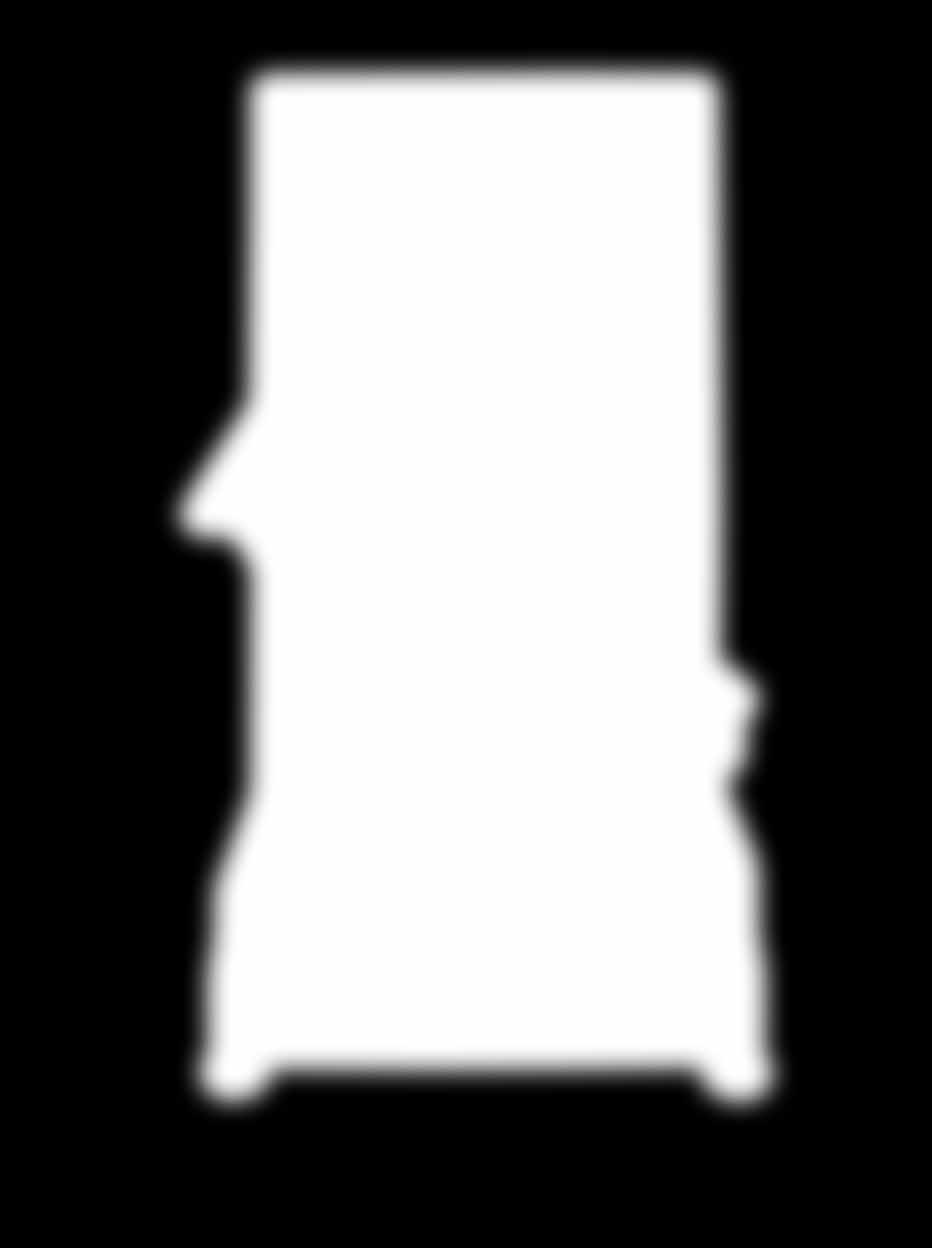
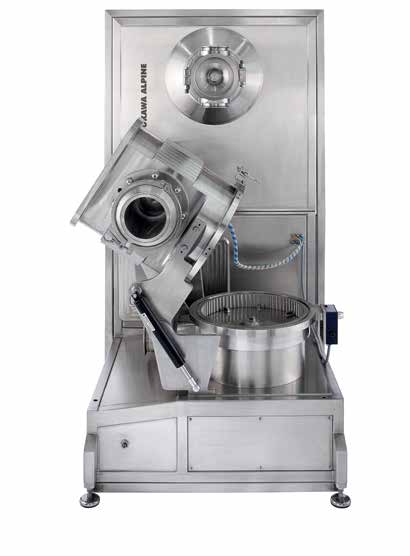
P h a r m a c e u t i c a l t e c h n o l o g y
GMP SIzE REDucTION SYSTEMS
PROCESS TECHNOLOGIES FOR TOMORROWSM
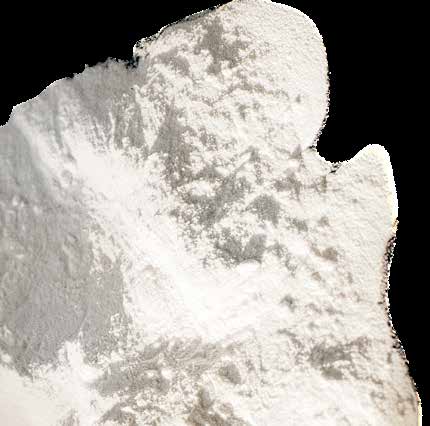

+++ Powder
and Particle
From millimetre to nanometre –
our service range
From milligram to tonne:
We develop versatile and efficient processing
innovative and sPecialised solutions
solutions for the size reduction/micronising of
For us, innovative technologies are state of the art. Our Pharma Division
pharmaceutical products. With many years of
leads the international market for powder processing equipment. We
experience, our team of engineers can offer
provide the entire range of size reduction technology, from deglomeration
you tried-and-tested, versatile concepts and
in the millimetre range right through to micronisation and nano-scale
standard solutions as well as special solutions
milling in the µm and nm range. We cater to R&D gram-scale requirements
tailored to your specific requirements.
as well as to production batches that weigh several tonnes.
our customers process the following
r&d – when every gram counts
products (examples):
The course of future production methods is set as early as the R&D
- Pharmaceutical substances of category
stage. Research laboratories need to work with technologies that are
OEB 1 - OEB 6 with resultant OEL values of
also available for later production processes. At this early stage, it is
between < 50 mg/m3 and < 200 ng/m3
important that research labs have the right equipment at their disposal.
- Excipients such as lactose, sugar, cellulose
We offer very small systems such as the Picoline machines for processing
- DPI (carriers and active substances)
gram-scale batches. They are based on well-established production lines
and provide customers with a high level of reliability, ensuring that the
- Nanopharmaceuticals
production method can easily be applied to the required production scale
- Hot-melt-extruded pharma polymers
at a later date.
multi-mill systems
Multi-processing systems are a speciality of the Pharma Division. These
systems comprise different mill types which share the same ancillary
equipment. These systems are not only extremely versatile, but they also
reduce capital expenditure and validation requirements to a minimum.
aPPlication areas oF diFFerent mill tyPes
Wet agitated media mill AHM
Spiral jet mill AS
Fluidised bed opposed jet mill AFG
classifier mills zPS/AcM
Fine impact mills uPz
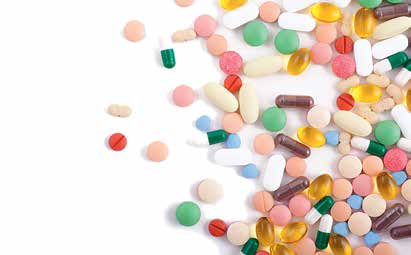
ciP / siP
cleaning In Place and Sterilisation In Place are highly exacting processes
which place stringent requirements on system design and engineering.
Our Pharmaplex® bearing assembly allows sterilisation with saturated
steam for high-speed, oil-free bearing concepts used in mills and metering
equipment.
containment
Increasingly exacting occupational safety requirements and the use
Passion For Pharma
of highly active pharmaceutical substances compel manufacturers
to reassess their system components. The integration of grinding
- Our systems comply with the most exacting
technology into isolators proved to be highly challenging and
international standards:
often turned out to be too complex for isolator manufacturers. As
- Product- and process-contact parts are made of
the responsibility for the complete system should lie with only one
AISI 316L stainless steel
single supplier, Hosokawa Alpine has been developing integrated
- Surface roughness standard Ra < 0.8 µm
containment milling systems for fifteen years. The benefits are obvious:
(depending on the project Ra < 0.4 µm or
our customers are supplied with complete solutions from one source
Ra < 0.25 µm with/without electropolishing)
that do not pose any integration problems.
- Seal and filter material suitable for use with
food and drugs according to FDA 21cFR177.2600
- Particle- and oil-free, clear separation between
Process safety and repeatability is ensured by monitoring and
drive and process thanks to pharmaceutical
controlling all relevant parameters. We also integrate in-line laser
diffraction systems made by different manufacturers into our systems.
- Encapsulated, permanently lubricated bearings
These allow monitoring and inspection of particle sizes.
or use of uSDA-H1 lubricant
- Fully cIP/SIP compatible machines thanks to
test and rental equiPment
patented Pharmaplex® bearing concept
Our state-of-the-art test centre equipment is available for customer
- Mostly monobloc components with a low
tests. However, many pharmaceutical chemicals are highly toxic and
number of welding seams and seals
cannot be sent to us for safety- or customs-related reasons. In these
- Design free of dead spots
cases, we offer our customers a wide range of rental equipment which
- Drainage and evacuation points for residual air
allow tests on the customer's site.
removal in cIP/SIP-compatible systems
- control according to GAMP 4/5 and 21 cFR Part
Wet-grinding at its finest
uPZ fine impact mills
Some like it coarse
acm/ZPs classifier mills
The dose makes the medicine
spiral jet mills
More than just accessories
Fluidised bed opposed jet mills
ultrafine and sharp top cut
Trust but verify
validation
unbeatable versatility
PROCESS TECHNOLOGIES FOR TOMORROWSM
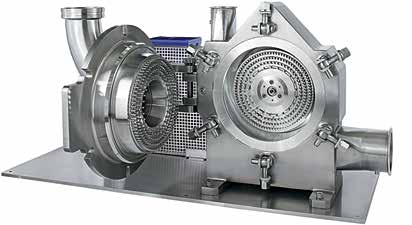
+++ Powder
Fine imPact mills
and Particle
uPZ – coarse to Fine
areas oF aPPlication
Metformin HCL - UPZ (Pin Disc)
Fine impact mills or universal mills are used for fine and ultrafine
grinding. Depending on the product, these mills cover a fineness range
of between appr. 30 µm and 1,500 µm. As this mill type can be used
with different grinding elements, it is very versatile. Thanks to the rotor's
ventilation effect, the product is conveyed and cooled at the same time.
The end products are low in fines and have good flow properties.
- Typical area of application: deglomeration/
milling for end-product fineness of between 30 µm and 1,500 µm
- Grinding of soft to medium-hard materials
- Highly versatile thanks to different
grinding elements
- cooling effect thanks to high air flow
- End products are low in fines
315 UPZ fine impact mill
Pharma range
PrinciPle oF oPeration
uPz mechanical impact mills are be employed, e.g. a pin disc or
designed for dry grinding soft to a plate beater unit with profiled
medium-hard materials. The feed grinding track or a sieve grate.
material is charged to the centre of
The fineness is set by adjusting
the rotor equipped with grinding the rotor speed and the feed rate.
Pz fine impact millu
Max. air flow rate* (m³/h)
elements and is comminuted
by impact against the rotor and stator elements. After passing
through the grinding zone, the
product enters the mill housing and is then discharged from the
mill by gravitational force. The
rotation generates an air flow from which the end product is
* Max. values, depending on grinding tools** Max. speed, depending on grinding tools
extracted and charged to a filter.
For R&D application
Different grinding elements can
Practical examPles
End-product
fineness
put kg/h size
Acetylsalicylic acid
Acetylsalicylic acid
Powder fineness in % < µm – measuring points of particle size distribution
All values are non-binding reference values only
- Pin discs – for very high end-product
the versatile uPZ
fineness or for homogenisation
- Plate beater unit – cooling effect thanks to
sterile milling system incl.
- Plate beater unit with sieve ring – particle
feeding screw PDD 35 in
CIP/SIP-able design
size limitation with low fines content
- Plate beater unit with grinding track –
comminution of hard material
- combination of grinding track and sieve for
better particle size control
- Grinding tracks available in different
geometries for optimsation
100 UPZ
cryogenic milling system
with Alpine KF 40
screw cooler
100 UPZ
isolator solution with integrated
in-line particle analysis
and PDD 25 screw feeder
PROCESS TECHNOLOGIES FOR TOMORROWSM
+++ Powder
and Particle
mikro acm + ZirkoPlex ZPs –
sharP toP cut
areas oF aPPlication
classifier mills are used for the ultrafine grinding of soft material with
an end-product fineness of appr. < 10 - 150 µm. They offer a range of
advantages over fine impact mills. The integrated air classifier gua-
rantees end products that are free of oversized particles with a steep particle size distribution and sharp top cut control. Grinding and se-
classifier mill vs. fine impact mill
paration parameters can be set independently for optimum results,
which ensures reliable product quality for the different particle sizes
or product properties required. The high air/gas flow cools the product.
distinction between acm + ZPs
During its corporate history, Hosokawa Alpine has developed two
different types of classifier mills, and both have become established
in their own right and have found their optimum area of application.
The Mikro AcM with its straightforward design is used all over the world in practically all industries, also in the pharmaceuticals segment.
- Typical area of application in the
pharmaceuticals industry is for particle sizes of between 10 µm and 150 µm
- Guaranteed top cut control thanks to
integrated air classifier
- Steep particle size distribution
- Optimum setting of grinding parameters
- cool grinding thanks to high air/gas flow
Pressure shock resistant
Maschine for Integration
Execution Easy Clan
in Cleanroom wall
Like the AcM, the pharma product chamber often allows execution of the AcM is a twin-
the comminution of sticky and
rotor classifier mill with a compact adhesive product. The classifier footprint that can be opened from
head of the zPS is identical
the top for easy access, inspection to that of Hosokawa Alpine's and cleaning. Thanks to its lean classifiers of the ATP range design, the AcM is inexpensive and is also used in simple air and cost-efficient in maintenance. classifiers or in combination The increased air flow allows with AFG fluidised bed opposed easy processing of heat-sensitive jet mills. This approach allows
70 ZPS isolator solution with PDD 25
metering screw
materials. In the pharmaceuticals the use of the zPS in so-called industry, the AcM is typically used multi-process systems. In this for the production of excipients set-up, the ATP classifier head and carrier materials, often in is the central component and mono-product systems with the grinding units for zPS, AFG continuous production or for large and ATP can be interchanged batch sizes.
very easily. The bearings for zPS the machine sizes from 50 zPS classifiers and mills are tried-
through to 200 zPS are popular
The zPS with its horizontal and-tested air-purged systems for very small API batches – also classifying wheel offers sharp top
which are available in a cIP/
for high active pharmaceuticals
cut control even when processing
SIP-compatible design. used by in contained installations.
challenging materials. The larger the pharmaceuticals industry,
Throughput
End-product fineness
Machine size
Powder fineness in % < µm – measuring points of particle size distribution
All values are non-binding reference values on
PROCESS TECHNOLOGIES FOR TOMORROWSM
+++ Powder
and Particle
For R&D application
mikro acm + ZirkoPlex ZPs –
sharP classiFier cut Point
Pharma range ZPs
PrinciPle oF oPeration
The zPS and the AcM are mechanical impact mills with an integrated
classifier designed for the dry fine grinding of soft to medium-hard
materials with a steep particle size distribution. comminution is performed by a high-speed rotating disc with grinding elements. The feed material is charged to the grinding chamber and is accelerated by
zPS classifier mill
ø grinding disc (m
Max. air flow rate
means of the grinding rotor. comminution is the result of the particles impacting against the grinding elements of the rotor and against
the grinding track. The grinding air flows through the grinding gap
between the rotor and grinding track from below, passes through a deflector vane ring and then flows through the classifying wheel located
in the mill head. The classifying effect of the classifying wheel means that fine particles are able to exit the mill entrained in the air and are
collected in a filter. coarse particles fall back onto the rotor and are comminuted further until the desired fineness is reached. The fineness
is set by adjusting the speeds of the grinding rotor and the classifying wheel as well as the air flow rate.
Pharma range acm
M classifier mill cA
Power classifier (kW)
Max. air flow rate
the versatile acm
200 ZPS detail
40 ACM classifier wheel
ACM 2 EC
in special Pharma design
the versatile ZPs
100 ZPS detail
70 ZPS Compact system installation
with PDD 25 metering screw and
PH-ZS 150 pharma-design
rotary airlock feeder
200 ZPS clean room
installation
PROCESS TECHNOLOGIES FOR TOMORROWSM
+++ Powder
sPiral Jet mills
and Particle
as - Just Fine!
Spiral jet mills are used for the easy to inspect and clean. As
ultrafine comminution of dry spiral jet mills do not generate pharmaceutical substances. heat during grinding, even
Typically, particle sizes in the heat-sensitive materials can be
range of < 5 – 40 µm are achieved.
comminuted without problems.
The benefits of spiral jet mills are Spiral jet mills are not suitable
in their simple design without are often not suitable for sticky
moving parts, which makes them products of for applications
are prone to sedimentation or
for applications that require a
controlled, steep particle size
distribution. For these cases,
we recommend fluidised bed
opposed jet mills. Smooth
- Typical area of application:
grinding of products with
micronising in the range of < 5-40 µm
agglomerates in the batch to be
- Simple design – easy inspection and cleaning
processed require pre-crushing.
- No moving parts
- No heat generation
- Pre-crushing to < appr. 2 mm is necessary
For R&D application
- Broad particle size distributionng
400 AS spiral jet mill
PrinciPle oF oPeration
Pharma range
The AS is a spiral jet mill designed desired fineness. The mill settings for dry grinding soft to medium-
can be adjusted by varying the
hard materials. A number of air grinding air flow rate, .air flow nozzles generate an air vortex that
rate and the grinding gas pressure.
rotates at high speed. The feed material is fed to the grinding
chamber via an injector assembly.
AS spiral jet mill range
Number of nozzles
Nominal air flow*
comminution is the result of
inter-particle collision caused by the different velocity gradients
in the air flow. The grinding air is extracted by means of a dip
pipe located in the centre of the grinding chamber. Because of the
free vortex, a classifying effect is
generated, meaning that only fine particles can exit the mill through
the dip pipe and be collected in a filter. coarser particles remain in
the grinding chamber until such time as they have reached the
* at grinding pressure of 6 bar g
100 AS detail
315 AS module with PDD 30 double
metering screw
Smallest AS for R&D processing of mini
batches at maximum output (mg + g) with
the Piconizer®
Isolator-integrated 100 AS
140 AS sterile system
Throughput
End-product fineness kg/h
Machine size
90 % < 2.4 µm
Disposable mill
97 % < 3.8 µm
97 % < 4.1 µm
97 % < 5 .2 µm
Plastic lining parts of the 100 AS
Powder fineness in % < µm – measuring points of particle size distribution
All values are non-binding reference values only
PROCESS TECHNOLOGIES FOR TOMORROWSM
+++ Powder
Fluidised bed
and Particle
oPPosed Jet mills
aFg – ultraFine and sharP
area oF aPPlication
In addition to the tried-and-tested spiral jet mills for the production
of ultrafine end products, fluidised bed opposed jet mills with
their special housing geometry and the integrated classifier offer a
significant technological benefit: the dynamic classifier ensures a high
separation accuracy for an absolutely pure top cut which is free of
oversized particles. changes in the fineness setting can be achieved
- Typical area of application:
easily and reliably thanks to the frequency-controlled classifier drive.
micronising in the range of < 4 µm – 150 µm
compared to spiral jet mills, this approach allows a very broad setting
- Accurate fineness setting
range of between about 4 µm and 150 µm (d97). This type of mill is
- Sharp top cut control
suitable for products that are prone to sedimentation.
- Steep particle size distribution
- No heat generation
PrinciPle oF oPeration
- Suitable for products of sticky or
The AFG is comprised of two components – the classifier head and
the grinding chamber with integrated nozzles, the number of which
- No abrasion/wear
depends on the mill size. The material particles entering the jets are
accelerated and collide with each other in the focal point where the jets of air intersect. comminution occurs due to inter-particle collision
Pharma range
in the focal point and because of shear flows at the edges of the air jets. As a result, the risk of contamination due to abrasion is virtually non-existent. A high-performance Turboplex classifier discharges the
end product from the internal grinding process to a separator system (cyclone or jet filter). The fineness can be set by adjusting the air flow rate, the grinding air pressure and the classifying wheel speed.
Fluidised bed opposed
jet mill range (AFG)
Nominal flow rate*
* at a grinding pressure of 6 bar g
280 AFG fluidised bed
opposed jet mill
200 AFG Installation
for pharma lactose
100 AFG Compact Pharma System
100 AFG Isolator integration
End-product
Throughput
fineness
Machine size
140 AFG - Installation in clean room wall
Salbutamol sulphate
Powder fineness in % < µm – measuring points of particle size distribution
All values are non-binding reference values only
PROCESS TECHNOLOGIES FOR TOMORROWSM
+++ Powder
and Particle
mPs – unbeatable versatility
area oF aPPlication
In the wake of the steady flow of newly developed products with
unpredictable grinding properties, mills have to offer maximum
versatility. This is the objective of so-called multi-mill systems, which
offer the perfect solution to changing requirements. Multi-mill systems
are mobile, very versatile concepts where two or more different mill
types are integrated into one ancillary installation, allowing a quick
change-over between the required units.
- Different mill types share the same
ancillary equipment
- Highly versatile for production
of different products
- Fast change-over
- Reduced capital expenditure
- Reduced documentation and
validation requirements
200 AFG 100 ZPS
multi-process modular system:
The following modules can be used alternately:
PrinciPle oF oPeration
- AFG fluidised bed opposed jet mill
The size of the installation is based on similar batch volumes,
- ATP ultrafine classifier
product throughputs, process gas flow rate, etc. The configuration
- zPS classifier mill
allows different metering systems, fittings, drives, product filters,
- AS spiral jet mill
ventilators, etc. to be used. The benefits are obvious: in addition
- uPz fine impact mill
to a high level of versatility – retrofitting is also possible – capital
expenditure, documentation and validation requirements are reduced to a minimum. Multi-mill system combinations can be used both on an R & D (Picoline®) and on a production scale.
Module 100 UPZ
Module 100 AFG
Disconnect 100 AFG
Detail technical area
Multimill Isolator Integration
100 AFG 50 ZPS Multi mill
Cone MillExchange of Mill Modules
within technical area of isolator
For R&D application
multi-mill –
combination oPtions
The ultimate
multi-mill
PROCESS TECHNOLOGIES FOR TOMORROWSM
+++ Powder
and Particle
agitated media mills
ahm – wet grinding
at its Finest
Grinding example: fenofibrate
wet grinding down to nanoscale siZe
The amount of poorly soluble pharmaceuticals among NcEs is on the
Particle Size (µ 0,3
increase. New drug delivery methods are required to help increase
the bioavailability of these substances. The ultrafine grinding of
particles down to nano-scale size with the help of agitated media
Specific grinding energy (kWh/kg)
mills is one way of improving their bioavailability. This approach opens up a range of additional benefits: accurate dispensing,
minimised volumes and fast effectiveness. The minimal volume of
- Grinding of insoluble APIs in the submicron and
nanosuspensions in syringes improves the injectability of the drug
and minimises sedimentation problems.
- Versatile, exchangeable wear protection
elements (ceramics, plastic) possible
- Easy to clean, GMP design
- Double-action mechanical seal
- Sterile equipment option
For R&D application
PrinciPle oF oPeration
Pharma range
The AHM is an agitated media mill designed for the continuous or batch-operated wet ultrafine grinding of particles in solution. The grinding chamber of the mill is usually filled with ceramic grinding beads which are set into motion by a rotating agitator. The feed product is suspended in a fluid and is conveyed through the grinding chamber by means of a pump. comminution is a result of the friction caused when the feed particles impact against the agitated grinding
Grinding chamber (l)
beads. In continuous operation, the suspension exits the mill after passing through the grinding zone, while a screening element retains
the grinding beads in the mill. The fineness level is set by adjusting the rotor speed, the filling ratio of grinding beads in the mill and the
suspension flow rate, as well as by selection of the grinding bead size.
Mill equipment in various
construction materials
agitated media mills
50 AHM
Picoliq
200 AHM
In pharma-design
90 AHM
Complete installation
Specific grinding
Machine size
50 AHM (Picoliq)
PROCESS TECHNOLOGIES FOR TOMORROWSM
+++ Powder
and Particle
some like it coarse
Pre-crushers: practical examples
Pharma-design ha 20/10 hammer mill
Pharma-design laboratory hammer mill for the size reduction and
disintegration of agglomerates and lumps producing an end-product
fineness of < 500 µm with minimum fines. Depending on the project,
the mill can be delivered integrated into an isolator.
- Disintegration of agglomerates and lumps
of up to <500 µm
- Processing of soft and medium-hard
- Easy cleaning/dismantling
- cantilevered bearing
- Purged pharma bearing
Pharma range
For R&D application
Rotor diameter (mm)
Number of beaters
Pre-crushers: Practical examPles
End-product
Throughput
97 % < 1.000 µm 70
50 % < 100 µm
Nacl (table salt)
DB pre-crushing range
Sieve grate gap* (mm)
Lumps of about 100 mm
* = depending on the application
Powder fineness in % < µm – measuring points of particle size distribution
All values are non-binding reference values only
db 500 Pre-crusher
crusher for soft, slightly
20/12 RO detail
crumbly materials and lumps. Ideal for disintegrating and aerating agglomerates and for
processing lumps. Typical areas of application include the size reduction of agglomerated excipients and additives after transport or storage. Easy and compact installation. Available with sieve grate gaps of 12 mm and 18 mm.
Pharma-design rotoPlex
ro 20/12 granulator
Pharma-design granulator for
pre-cutting pharmaceutical and
chemical products. The granulator
has a twin-knife rotor and a three-
knife stator. A range of different
Pharma range
screen inserts allows definition of the maximum top cut.
Rotor length (mm)
Maximum rotor speed
* = depending on the application
Practical examPles rotoPlex
End-product
Throughput
Machine size
- Size reduction of materials
Medicinal herbs, stalks
suitable for cutting such as
Medicinal herbs, flowers
medicinal herbs, fibres, and
polymers to end-product fineness < 1 – 2 mm
96 % < 3.15 mm
- Pharma/GMP-qualified design
Granulated pharma
16 % < 250 µm;
- compact footprint
Powder fineness in % < µm – measuring points of particle size distribution
All values are non-binding reference values only
PROCESS TECHNOLOGIES FOR TOMORROWSM
+++ Powder
and Particle
metering systems – it all
dePends on the dosage
- GMP-qualified design
Pdd Pharma double Feed metering screw
- Modular configuration
- clear division between product-contact
Hosokawa Alpine develops its
own system components to
- Easy to dismantle, i.e. easy to clean the
suit the special requirements
product-contact zone
of pharmaceutical applications
- Product-contact components can be
and guarantee the compliance
autoclaved when pre-assembled
- Optional volumetric or gravimetric metering
The ALPINE PDD double feed
- Special design for isolator integration
metering screw is a twin screw
in continuous operation for the accurate metering of dry substances. The complete screw
Feed screw range
comprises the following modules:
- different agitator and screw
geometries available
Filling station with PDD
- volumetric and
35 (SIP) for isolator
gravimetric design
- containment solution
for isolator integration
Module 1 – drive unit
Screw drive with Dc motor, fully integrated into a stainless-steel housing.
Module 2 – bearing unit
Screw bearing in closed monobloc
housing with bayonet catch and
lip sealing.
Module 3 – product container
Screw housing in monobloc
design with integrated mixer.
Pharma micro dosing screw Pmd
We offer metering solutions especially for pharmaceutical applications.
Minimum metering rates and residue-free dosage of very small batch
sizes is a major challenge.
The ALPINE PMD micro dosing screw is a volulmetric feeder in
continuous operation for the accurate metering of minute volumes
and is suitable even for substances with poor flow properties. The
special design reduces product residues to a minimum.
Pharma – Pdr metering channel
The ALPINE PDR is a volumetric vibration feeder in continuous in con-
tinuous operation for the accurate metering of free-flowing products.
range oF vibration Feeders
Open vibration chute - for lab applications
closed vibration pipe Ø 32 mm
Micro Dosing Screw
closed vibration pipe Ø 100 mm
PDR
feed chute
PDR 32
Vibration pipe
PDR 100
Vibration pipe
PROCESS TECHNOLOGIES FOR TOMORROWSM
+++ Powder
and Particle
more than
Just accessories
Zs 150/200 rotary valves
ALPINE zS 150/200 rotary valves are used as rotary
feeders, discharge devices, barriers for pressure-
shock-proof installations and air/gaslocks. They
are specially designed for compliance with cGMP
requirements and are therefore characterised by
their ease of dismantling and cleaning. They also
allow force purging of bearings and housing covers.
ZS 200
Installation in
clean room wall
- cGMP-qualified design
- Modular configuration
- clear division between product-contact
- Easy disassembly, i.e. easy cleaning
of all product-contact areas
- Product-contact components can
be autoclaved when pre-assembled
- 10 bar pressure-shock-proof and
flameproof designse
- Gas-purged bearing and housing cover
- Alternative rotor chamber sizes
range oF rotary valves
* clamp DIN 32676
DN 50 EzConnect
alPine eZconnect comPensators
dn 50 – dn 300
Hosokawa Alpine's compensators are made from a single piece of silicone and a hygienic tri-clamp connection as an additional part.
other Features:
- Suitable for operating temperatures of between -20°c and +140°c
- Explosion protection: suitable for use up to zone 20
- Suitable for operating pressures of between -0.25 bar to +0.5 bar
- Simple, hygienic tri-clamp connection
- clamp connections made from stainless steel AISI 316 L
- The compensator is made either of EPDM or silicone and complies
with FDA directive 21 cFR § 177.2600
- The support rings are a principal part of the compensator- (no loose parts, very easy assembly)
Installation length max. compensation Diameter
PROCESS TECHNOLOGIES FOR TOMORROWSM
+++ Powder
and Particle
trust, but veriFy
Process automation
Autmation by Hosokawa Alpine is process technological expertise
translated into software and hardware. A team of experienced
electrical engineers develops the basic principles of our automation
technology and ensures the perfect interaction of all module interfaces
and end-to-end documentation of all modules.
Process visualisation
The process sequences and process parameters are represented
Hosokawa Alpine offers optimal process solutions.
graphically on-screen. The system flowchart forms the basis of process
Process technology and automation engineering are
display; it is formatted, animated and supplied with the required
tailored to customer requirements and come from
process parameters. It is important that the flowchart is easy to read
one single source.
and that process sequences are easy to follow. colour-coding is used
system automation has significant
to highlight important information, while less important information
is displayed in the background. The process is also operated on-screen.
- Overview of the complete system condition at
The user interface has a simple, logical design, user navigation of the
menu structure is highly intuitive. This prevents operating errors and
- Menu navigation for the operating modes
avoids additional training requirements.
- Process operation
- cleaning operation
exPertise in Process engineering
Process engineers and electrical engineers cooperate in developing the
- Process data memory
best solution for each customer. Modular automation components are
- Trend visualisation
individually combined, depending on the process and the customer's
- Alarm archiving
automation requirements. customers benefit from our process
- Password administration
- Recipe management
- configured in compliance with
GAMP 4/5 and 21 cFR Part 11
count on us!
upon receipt of the uRS, the characteristic process data such as the end-product fineness and throughput rate, etc.
The user Requirement Specification
are determined, and the system-specific parameters such as
(uRS) provides us with the customer's
construction materials and surface qualities, etc. are defined.
main system specifications, i.e. the
The resultant system configuration is checked during the
grinding system requirements.
subsequent qualification phase for compliance with the uRS.
Process imPlementation
alPine testing centre
alPine rental equiPment
Alpine's testing centre offers unique facilities for carrying Following acceptance of the layout, manufacturing drawings
out customer trials aimed at finding the best possible system are prepared and, if required, special solutions are developed.
design and at determining the technical warranty parameters.
If occupational safety restrictions prohibit the processing of manuFacture / assembly
materials at the testing centre, we can offer a range of rental Manufacture, assembly, wiring and connection to the control
systems which can be installed and operated at the customer's unit are carried out on Alpine's premises, which ensures the
site. This way, customers can gather their own experience with
perfect interaction of all interfaces.
the machines and compile their optimum uRS.
design study
The executed quality of the system is inspected by means of
Based on our experience and in close cooperation with our factory and site acceptance tests (FAT/SAT). compact systems customers, we develop a system concept which is tailored to the
are completely assembled on Alpine's premises and subjected
customer's requirements and which illustrates ergonomic aspects.
to a FAT, which reduces the effort for the SAT to a minimum
commissioning / training
This service is available if required, e.g. for complex projects Alpine supports its customers during system commissioning and involving isolators, we create a 1:1 wooden model that allows
provides training for the operating personnel.
simulation of all important process steps with original components wherever possible.
PROCESS TECHNOLOGIES FOR TOMORROWSM
+++ Powder
and Particle
1. Powder and Particle Processing
Hosokawa is the world's largest supplier of processing systems for
Hosokawa Alpine has been in business for
the powder and particle processing segment. Renowned names
more than 100 years, and we have been
such as Alpine, Bepex, Stott, Vitalair, Rietz, Mikro, Micron and
setting the standards, regardless of the
Vrieco-Nauta are all part of the group's product range. Regardless
segment, be it blown film production or
of the size, be it production-scale system, pilot system or laboratory
powder and particle processing. The chal-
equipment, Hosokawa's products and technologies are used at
lenges of market leadership and our ex-
numerous production stages, e.g. for size-reduction, mixing, drying,
perience inspire us to aim for a constant
agglomeration, classification, weighing and metering.
refinement of our technologies.
2. blown Film lines
Hosokawa Alpine is one of the world's foremost suppliers of blown
film lines. Alpine supplies complete systems for blown film production
and processing from a single source, from granule feeding systems to
film winders, from single-layer die heads to 7-layer lines, from simple
speed regulators to state-of-the-art process control systems. Thanks to
Alpine's film orientation lines, the company can now offer complete
systems for film conditioning.
3. conFectionery & bakery technology
Benefiting from the vast expertise of companies such as Bepex, Kreuter
and Ter Braak, Hosokawa confectionery and Bakery is the ideal partner
for the confectionery industry. A complete range of machines and
production systems is available or can be tailored for the requirements
of every stage of the production chain, from preparation of the raw
materials and confectionery pastes to the end product.
Process technologies For tomorrowsm
divisional structure
The name Alpine stands for expertise in all areas of size-reduction technology. After many years of close
cooperation between our engineers and our customers' R&D departments, we have become the world's
leading specialist for powder and particle processing. In order to ensure that customers from different
industrial segments receive professional assistance and consultancy, our particle processing division is
divided into five subdivisions:
Pharma & lab
minerals & metals
Producing powdery substances for the We provide complete dry and wet processing pharmaceuticals industry requires the skills and systems with state-of-the-art mills and classifiers for experience of experts. Hosokawa Alpine complies processing mineral raw materials. Our machines and with international pharmaceutical standards and systems for processing fillers, ceramic raw materials, supplies a wide range of products and services, metallic compounds and alloys meet the exacting including laboratory applications and special requirements of our customers.
processes. Whatever size reduction method is required, we are the specialists.
recycling & granulators
We design, engineer and deliver complete granulator
systems which include all required system components.
The range of chemical products is as diverse as the Be it for injection-moulded parts, sprues, film webs different demands on pigment or powder properties.
and edge trimming, our granulators are designed for
We provide process engineering solutions for the the most challenging tasks.
chemicals industry from a single source. We also
offer competent consultancy on basic chemical Food
products and auxiliaries, toners, paints, pigments, The food division develops special food processing
herbicides and fertilisers.
techniques and supplies complete production lines for sugar, cocoa, lactose, proteins and spices.
service
Our service division provides support throughout
the entire life-cycle of Hosokawa Alpine systems
or machines. Our comprehensive service package
includes spare parts supply, servicing, inspection,
maintenance, repair, general overhauls, system
upgrades and training. A recent addition to our
service range is the supply of pre-owned Alpine
machinery.
Hosokawa Alpine is at your service – no matter
where you are and what your processing challenge
is. Our service range includes project management,
installation, commissioning, training, maintenance
and system optimisation.
PROCESS TECHNOLOGIES FOR TOMORROWSM
HOSOKAWA ALPINE Aktiengesellschaft
P.O. Box 10 11 51
Address for visitors and deliveries:
Peter-Dörfler-Strasse 13 – 25
+ 49 821 5906-283
+ 49 821 5906-620
Subject to change without notice. All data in this
brochure are purely informative and without
guarantee as to correctness. Authoritive for
orders are our quotations.
Hosokawa Alpine is a member of the Hosokawa Micron Group, a high-perfor-
mance manufacturer of systems for powder and particle processing, systems
for the confectionery industry as well as plastics processing machines and
systems. The group is known and reputed the world over for its power of inno-
vation, constant product care and market-oriented R&D. The most important
group resources are R&D, engineering and manufacturing as well as customer
service in all global markets.
Hosokawa Alpine 2013. Printed in Germany.
Pharma 04.13/1(EN)
Source: http://www.teknol.eu/wp-content/uploads/2013/12/Pharmaceutical-technology-GMP-size-reduction-systems1.pdf
Authored by the DIGITAL DERMATITIS (HEEL WART) Digital dermatitis (DD) is a multi-factorial superficial dermatitis of thedigital skin of cattle. The mostcommon site is the palmar/plantarinterdigital ridge of the foot—especially the rear feet (Figure 1),but other sites include the skin of theinterdigital cleft, the heel, sometimesunder-running the sole, and thedorsal aspect of the coronary band(Figure 2), where they may beassociated with a vertical wall crack.
Journal of Aquatic Biology and Fisheries Vol. 2/2014/ pp. 133 to 140 ANTIDIABETIC AND ANTIOXIDANT ACTIVITY OF PADINA TETRASTROMATICA IN HIGH CALORIE FED/STREPTOZOTOCIN TREATED RATSDivya S. Mohan, Mini Saraswathy, Muraleedhara Kurup and Gopala Kurup* Department of Biochemistry, University of Kerala, Kariavattom Campus,