Lauri: what the table of directive analyses is serving

Substitution of trichloroethylene as cleaning
solvent in metal processing
This case study aims to illustrate a chemical substitution process. It is based on publicly available information on company's experience as well as on substance hazards, alternatives to the hazardous substance and regulatory information. The case study is neither complete nor comprehensive in illustrating all substitution options of a
substance but rather exemplary.
1. Case description
Trichloroethylene is a colorless, volatile, inflammable solvent, which has a sweet odor and is hazardous to human health.
Synonyms for Trichloroethylene: Acetylene trichloride, Ethinyl trichloride, Trichloroethene,
Trichloroethylene, Trilene, Triklone®, Trimar. Industrial abbreviations include
trichloroethylene, trichlor, Trike, Tricky and trichloroethylene. 1.1 Hazards of Trichloroethylene (TCE)
Trichloroethylene (CAS number: 79-01-6; EC-number 201-167-4) is classified (harmonised) as a substance that may cause cancer, serious
eye and skin irritation and may cause drowsiness or dizziness. It is suspected of causing genetic defects and it is also harmful to aquatic life
with long lasting effects.
Additionally, the classification data provided by companies for ECHA in
REACH registration process identifies that this substance may cause an allergic
skin reaction. Some notifiers also classified it as respiratory sensitiser.
TCE evaporates very quickly and contributes to the formation of ground level ozone (summer smog).
Regulatory status
Trichloroethylene is a so called Substance of Very High Concern (SVHC). It is
included in the candidate list for authorization and requires authorization (since
April 21 2016) before it can be used
Workplace Regulations/OELs: at EU level an Occupational Exposure Limit (OEL) (8-hour TWA) for TCE is 10 ppm with a Short-Term Exposure Limit (15 min) of 30
Restrictions: Consumer uses are prohibited EU-wide, due to the TCE classification
as a carcinogen. Because of the use limitations and the authorisation, the number of suppliers of TCE may decrease in the long run.

2 Substitution process
2.1 Substitution incentives
In company „X", which performs metal processing, the subsequent washing and degreasing of parts, the manufacture process includes the use of
trichloroethylene. Since in the manufacture system trichlorethylene has to be periodically replaced, wastes, metal powder containing sludge and oils
accumulate and have to be disposed of by the company.
Main reasons for implementing substitution in this company were:
Authorisation under REACH – it was not clear if authorisation for the
specific use will be granted
Possibility to avoid negative impact for workers and environment
(emissions of VOC);
Possibility to reduce costs for waste management;
Possibility to unify the products used in deburring and cleaning parts;
Possibility to reduce the handling of parts between the different stages of
2.2 The substitution project
2.2.1 Identification of alternatives
Experience
Among the proposed alternatives there are other chemical substances that have
hazardous classification. Main alternative – non chemical aqueous technology, which must be combined with the correct equipment and can be just as effective as solvent cleaning. There are also such technologies as plasma cleaning or dry
ice blasting. All these alternatives were evaluated by the environmental expert and purchasing department.

Results – initial list
Alternative chemicals
Perchloroethylene
Methylene chloride
Hydrofluorocarbons (HFC)
Hydrofluoroether
Non chemical alternatives
Aqueous technology
Dry ice blasting
How to move on
As next step, the company decided to make specific requests to their suppliers by writing and with a follow-up call. They enquired if suppliers could provide the alternatives they offer, what is their willingness to cooperate and what is the cost
of implementation or/and product.
2.3 Selected alternative and justification
Preliminary assessment of the identified substances, based on their toxicological, ecological and technical performance was made. The results of their screening
assessment are shown in the following table.
Lack Comment
on hazard
source toxicity STOT CMR tisation
limitations
Perchloroethylene
(CAS No. 127-18-4)
Methylene chloride
(CAS No. 75-09-2)

Lack Comment
on hazard
source toxicity STOT CMR tisation
limitations
n-propyl bromide
(CAS No. 106-94-5)
Hydrofluorocarbons
Hydrofluoroether
From the gathered information about the hazardousness of proposed alternatives we see that only hydrofluorocarbons and hydrofluoroether could be tested. Other substances have been excluded because of their CMR properties.
After consultation with specialists from Environmental Protection Agency it was clarified that an additional registration in databases is needed for users of hydrofluorocarbons and hydrofluoroether. It was also stated that from the
environmental point of view, the use of substances that are involved in ozone depletion is not the best solution.
From the financial perspective all of the proposed chemicals were more
expensive 1-50%. Installation of plasma cleaning technology would cost 150 000 Eur, installation of dry ice blasting would cost 85 000 Eur, installation of aqueous technology would cost about 80 000 Eur.
After evaluation of all alternatives, a non-chemical alternative - aqueous technology was chosen for implementation.

2.4 Implementation
Implementation plan
Process evaluation when water based cleaning machine is used:
Although fresh aqueous cleaning solutions are usually classified as non-hazardous, they may accumulate enough contaminants during the cleaning process such as metal powder or oil and grease. As a result, it could be classified
as hazardous waste when disposed. Chemical analysis should be performed to determine the spent aqueous cleaning solution waste classification. Spent solutions are typically treated in an on-site wastewater treatment system or
shipped off site for disposal.
It must be taken into account that in some cases aqueous systems have the
disadvantage of much higher energy demand. For example if dry parts are required, and due to the non-universal material compatibility (combined cleaning of different materials is restricted).
State of play
The company's substitution action included the installation of a cleaning machine at the exit of each deburring device. The machines use a water-based, non-toxic
cleaning agent (96% de-ionized water). This product can be used as a cleaner and as a lubricant /coolant in deburring processes. This eliminates the use of cooling oils in deburring.
The new cleaning machines use a system to separate cutting and deburring fluids from metal powder originating in the deburring process. This extends the lifetime of the cleaning product considerably, which is recycled after cleaning to be used
as a deburring lubricant.
2.5 Communication of substitution
It was decided in company not to make specific communication of substitution as the qualities of the end product remained unchanged and customers would not be
affected by the changes.

2.6 Costs and savings
It was also made evaluation of costs
Process with TCE
Aqueous process
Balance on material
Trichloroethylene consumption
Coolant consumption
Consumption of new cleaning compound
Economic balance
Trichloroethylene consumption
Coolant consumption
Disposal of Trichloroethylene
Disposal of Trichloroethylene sludge
Consumption of new cleaning compound
Total savings
Investment
Return on assets
2.7 Evaluation
Investment costs pay off after 5 years and workers safety is significantly improved.
If treated in WWTP, it is wastewater and the metal and grease contaminations should be removed (and disposed of).

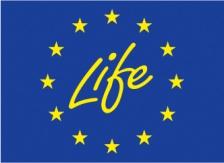
3 References
ECHA. 2016. Substance Information – Trichloroethylene. Available at:
(viewed in September 2016).
European Chlorinated Solvent Association (ECSA). Trichloroethylene: Legislation,
Markets and Uses. Mastering Challenges and Increase Sustainability. Available at: (viewed in September 2016).
Merit Partnership Pollution Prevention Project for Metal Finishers. 1997. Finding
an alternative to solvent degreasing. Ultrasonic aqueous cleaning. Available at:
(viewed in September 2016).
SUBSPORT. 2013. SUBSPORT Specific Substances Alternatives Assessment –
(viewed in September 2016).
SUBSPORT. 2016. Removal of trichloroethylene in the manufacture of metal parts.
Available at: (viewed in
September 2016).
The project "Baltic pilot cases on reduction of emissions by substitution
of hazardous chemicals and resource efficiency" (LIFE Fit for REACH,
No. LIFE14ENV/LV000174) is co-financed with the contribution of the
LIFE financial instrument of the European Community.
Source: http://www.fitreach.eu/sites/default/files/editor/Images/publiacations/Case%20story_Trichloroethylene.pdf
MANUAL DE ACTUACIÓN MANUAL DE ACTUACIÓN Dr. Francisco Toquero de la TorreVicesecretario OMC. Dr. Miguel Muñoz-NavasDirector del Servicio de Digestivo. Clínica Universitaria de Navarra. Pamplona. Dr. Fernando Gomollón GarcíaMédico Adjunto. Servicio de Aparato Digestivo. Hospital Universitario Lozano Blesa. Zaragoza. Profesor Asociado. Facultad de Medicina. Zaragoza.
Curriculum Vitae Priv. Doz. Dr. Siegfried Wieshammer Geburtsjahr: 1954 Tätigkeit: Chefarzt der Kardiologie, Pneumologie, Angiologie und Intensivmedizin, Ärztlicher Leiter des Pneumologisch-Thoraxchirurgischen Zentrums (PTZ) am Ortenau Klinikum Offenburg-Gengenbach Gebiet, Teilgebiet und Schwerpunktkompetenzen: Facharzt für Innere Medizin, Kardiologie, Pneumologie, Spezielle Internistische Intensivmedizin Studium: 1974-1980 Studium der Humanmedizin an der Ludwig-Maximilians-Universität